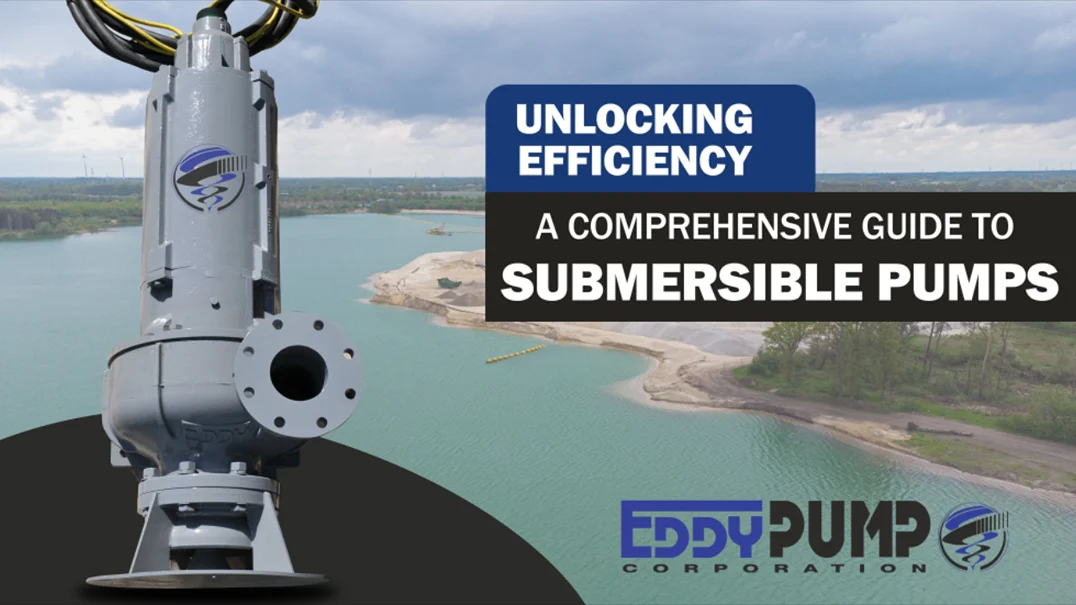
Looking to transform the way your company handles excessive flooding and slurry buildup? Consider industrial submersible pumps, designed to transform fluid handling in various industries and residential settings. These pumps operate fully submerged, eliminating the need for pump houses and reducing installation costs.
Submersible pumps find applications in draining flooded zones, handling sewage, extracting well water, and more. Their ability to manage diverse liquid types makes them indispensable in industrial and residential contexts. In this article, we dive into the world of submersible pumps to unlock their potential for your fluid handling needs.
What is a Submersible Pump?
A submersible water pump is a specialized fluid handling device engineered to operate while fully submerged in the liquid it is tasked with moving. This design eliminates the need for a pump house or suction lift, commonly necessary in non-submersible setups, thereby enhancing operational efficiency and diminishing installation expenses.
The primary components of a submersible water pump include an electric motor, an impeller, and a pump casing. The motor is hermetically sealed and intimately integrated with the pump structure, ensuring it remains impermeable and shielded against fluid ingress, which can result in electrical failure. This motor actuates the impeller—a rotor devised to escalate the kinetic energy of the fluid. The impeller’s configuration may vary (e.g., open, semi-open, or closed) depending on the application specifics and the fluid characteristics.
Submersible pumps are deployed in various scenarios, including industrial sump pump applications, draining flooded zones, handling sewage, extracting well water, and operating in oil wells. These pumps are particularly advantageous in scenarios demanding high head or pressure and involving pumping surface, deep, or water from significant depths.
Their operational adeptness, combined with the capacity to manage diverse liquid types—from pristine water to dense slurry—makes submersible pumps exceedingly valuable in both industrial contexts and residential setups. Submersible slurry pumps are tailored explicitly for handling abrasive liquids with high solid content, enhancing their utility in rigorous environments. The inherent submerged operation of these pumps also reduces noise pollution and conserves space, augmenting their suitability in densely populated or acoustically sensitive areas.
Understanding Submersible Pumps:
-
Design of a Submersible Pump:
A submersible slurry pump is meticulously engineered to handle abrasive materials within liquid mixtures, making it essential in mining, dredging, and heavy industry sectors. The principal design components of a submersible pump include a robust electric motor, a high-efficiency impeller, and a durable pump casing, all crafted to endure the strenuous demands of slurry transportation.
The electric motor in a submersible pump is hermetically sealed within a watertight compartment to safeguard against the ingress of liquids and solids, a critical factor in maintaining the submersible slurry pump’s electrical integrity and operational reliability. This motor is directly coupled to the impeller, which optimizes energy transmission and reduces mechanical losses, enhancing the system’s overall efficiency.
Constructed from abrasion-resistant materials such as high-chrome alloys, the impeller is the dynamic component that accelerates the slurry. It operates on centrifugal force principles, whereby rotation of the impeller forces the slurry radially outward from the pump’s center to its periphery, thereby elevating the slurry’s pressure and enabling its ascent through the discharge pipe.
The submersible pump casing is specifically designed to handle the abrasive, turbulent flow of the slurry. It is shaped to maximize flow dynamics and minimize wear, often equipped with replaceable liners made from durable materials like rubber or specialized alloys to extend the pump’s lifespan.
Overall, the design of the submersible slurry pump focuses on robustness, operational efficiency, and the capacity to manage dense, abrasive mixtures. This makes it vital in industrial sump pump applications, ensuring reliable performance in challenging environments.
-
Submersible Pump Inner Workings Explained
Motor and Impeller Integration: The industrial sump pump features an integrated electric motor and impeller within a compact, hermetically sealed unit. This integration allows the submersible pump to function efficiently while fully submerged in industrial sump environments, where continuous water removal is critical.
Direct Coupling: The electric motor is directly coupled to the impeller in the submersible slurry pump. This direct connection provides superior energy transfer from the motor to the impeller, reducing energy losses commonly seen in belt or chain-driven systems and enhancing operational efficiency in harsh industrial settings.
Centrifugal Force Mechanism: When activated, the industrial sump pump’s motor drives the impeller at high speeds. The impeller blades exert centrifugal force to expel water from the center of the submersible slurry pump to its periphery, optimizing fluid dynamics for adequate sump drainage.
Fluid Acceleration and Pressure Increase: The design of the submersible pump casing and the rotation of the impeller in the industrial sump pump accelerate the water, boosting its kinetic energy and pressure. This process is essential for pumping water vertically through the discharge pipe, overcoming the gravitational pull in deep sump applications.
Prevention of Cavitation: Operating fully submerged, the industrial sump pump minimizes the risk of cavitation, a problem prevalent in pumps with significant elevation differences between the submersible slurry pump and the water surface. Cavitation can lead to inefficiency and damage; thus, submersion is beneficial in preventing these issues.
Applications in Diverse Environments: Industrial sump pumps are designed to handle various challenging applications, from draining large volumes of water in industrial sumps to managing effluents and runoff in factories. The ability of the submersible slurry pump to operate while submerged ensures high efficiency and reliability, which is critical for maintaining operational continuity in industrial facilities.
Types of Submersible Pumps:
Submersible pumps are diverse in their designs and applications, tailored to specific operational requirements and environments. Here’s a breakdown of the different types of submersible pumps:
-
Submersible Water Pumps:
These pumps are designed to move water efficiently without large particles or contaminants. They are versatile and used in various settings, such as drainage systems, pools, and utilities.
-
Submersible Slurry Pumps:
This submersible pump is built to operate while submerged in abrasive slurry mixtures. It is essential in mining, dredging, and construction, handling materials like sand, gravel, and other debris. Its design includes features like vortex impellers to manage larger solids effectively.
-
Borehole Pumps:
These submersible pumps are engineered for deep underground applications, particularly in narrow, deep wells known as boreholes. They are equipped with powerful motors and hydraulic systems to draw water from deep sources, which is crucial in agriculture and industrial processes.
-
Oil-Filled Pumps:
Common in agriculture for lifting water from wells, these submersible pumps have motors cooled by surrounding oil, allowing them to operate in colder environments without freezing.
-
Stainless Steel Submersible Pumps:
Known for their durability and corrosion resistance, stainless steel construction enhances their longevity and performance. They are suitable for environments exposed to corrosive liquids.
-
Submersible Utility Pumps:
These compact and portable pumps are invaluable in construction sites and emergencies. They can drain flooded areas, empty pools, and transfer liquids.
-
Booster Pumps:
These submersible pumps increase water flow and pressure in systems where it is inadequate. They can be employed in residential, commercial, and industrial settings to ensure adequate water supply.
-
High-Temperature Submersible Pumps:
These are designed to handle fluids at elevated temperatures and are well-suited for specific industrial applications requiring heat-resistant operations.
-
Submersible Irrigation Pumps:
These submersible pumps are predominantly used in agriculture. They efficiently deliver water to crops and can lift significant volumes from deep sources.
Each type of submersible pump is designed with specific features to meet the demands of various environments and materials, ensuring efficient and reliable operation across a wide range of applications.
Applications of Submersible Pumps:
Submersible pumps, particularly the submersible slurry and industrial sump pumps, are integral to numerous critical applications across various sectors. Here are the primary applications of the submersible pumps:
-
Wastewater Management:
Industrial sump pumps are extensively employed in wastewater treatment facilities. These pumps are adept at handling solids and liquids, making them perfect for moving wastewater, including debris, organic waste, and other particulates.
-
Mining and Dredging:
The submersible slurry pump is essential for transporting abrasive and dense slurries in the mining industry. These pumps are used for tailings management, pond dredging, and sediment transport and provide robust performance in harsh mining and dredging environments.
-
Oil and Gas:
Submersible slurry pumps play a critical role in offshore drilling operations in the oil and gas sector. They efficiently manage abrasive materials such as drilling mud and ensure uninterrupted extraction processes by removing by-products from the drilling site.
-
Construction and Infrastructure:
Submersible slurry pumps are crucial for construction projects, particularly for dewatering large-scale excavations and developments. They effectively manage groundwater and surface water to keep construction sites dry.
-
Environmental Remediation:
Submersible slurry pumps are used in environmental cleanup projects to remove contaminated water, sludge, and other pollutants. Their robust design enables them to handle hazardous materials, aiding ecosystem restoration and pollution control.
-
Agriculture and Irrigation:
Industrial sump pumps support agriculture by facilitating efficient irrigation. They draw water from deep sources to deliver the necessary volume and pressure for uniform water distribution across expansive agricultural fields.
Benefits of Submersible Pumps:
Submersible pumps, including submersible water, slurry, and industrial sump pumps, offer several advantages over traditional pumps, especially when handling complex and demanding pumping tasks. Here are some of the critical benefits of these pumps:
-
Efficient Operation:
Submersible pumps, mainly submersible water pumps, operate by pushing fluid rather than pulling it. This method is highly efficient as it leverages the head of liquid where the pump is submerged, utilizing the surrounding pressure to assist in pumping. This efficiency reduces the energy required compared to traditional pumps that must draw liquid into their systems.
-
Enhanced Cooling and Protection:
Submersible pumps’ submerged operation ensures the surrounding fluid consistently cools the motor. This extends the motor’s lifespan and prevents overheating, a common issue in non-submerged pumps.
-
Reduced Cavitation Risk:
Submersible pumps are less likely to experience cavitation, which can significantly damage pump components. Being submerged, these pumps maintain the necessary pressure levels to prevent the formation of vapor bubbles that cause cavitation.
-
Versatility in Applications:
Submersible slurry and industrial sump pumps can handle various media types, including clean water, dirty water, oil, and abrasive slurries. This versatility makes them suitable for multiple applications, from drainage and sewage systems to complex industrial processes.
-
Low Maintenance and Installation Costs:
Submersible pumps are compact and do not require extensive installation setups like pump houses, making them more accessible and less costly to install and maintain. Their streamlined design minimizes the physical space needed for operation, a significant advantage in crowded or limited-space environments.
-
Improved Safety:
Submersible pumps minimize the risk of leaks or exposure to hazardous materials, as all components are securely contained within a single sealed unit. This feature enhances safety, particularly in applications involving hazardous or contaminated fluids.
Maintenance of Submersible Pumps:
Maintaining submersible pumps, including submersible water pumps and submersible slurry pumps, is crucial to ensure their longevity and optimal performance. Here’s a detailed explanation of how to maintain these pumps for extended and cost-efficient operations:
-
Routine Inspection:
Regular inspections are essential for early detection of potential issues. Inspect the submersible water pump and slurry pump for signs of wear or damage, such as cracks, corrosion, or abnormal noises during operation. Check the electrical cables and connections for any signs of deterioration or leakage.
-
Cleaning:
Submersible slurry pumps, which often operate in environments with high particulate matter, should be cleaned regularly to prevent clogging and debris buildup. This involves removing the pump from its operating environment, disassembling it if necessary, and cleaning all accessible parts with appropriate cleaning agents.
-
Impeller Adjustment and Replacement:
The impeller is a critical component that can affect the pump’s efficiency if worn or misaligned. Check the impeller periodically for any signs of damage or excessive wear. Adjust or replace the impeller to maintain the optimal performance of the submersible water pump or submersible slurry pump.
-
Seal Replacement:
The seals of a submersible pump protect its electrical components from water ingress. To prevent leaks and potential motor failure, these seals should be inspected regularly and replaced if they show signs of wear or damage.
-
Lubrication:
Some submersible pumps, especially those with bearings and other moving parts, require regular lubrication to ensure smooth operation. Use the recommended lubricant and follow the manufacturer’s guidelines regarding the frequency and quantity of lubrication.
-
Electrical Testing:
Perform regular electrical tests to ensure the integrity of the pump’s motor and control system. This includes checking the insulation resistance and voltage testing to detect potential electrical failures before they lead to more significant issues.
-
Performance Monitoring:
Monitor the performance of the submersible water pump and submersible slurry pump regularly to ensure they operate within their designed parameters. Look for any changes in flow rate, pressure, or energy consumption that could indicate underlying problems.
-
Documentation and Record Keeping:
Keep detailed records of all maintenance activities, including inspections, part replacements, and repairs. This documentation will help track the pump’s history and predict future maintenance needs, enhancing the preventative maintenance strategy.
By following these maintenance procedures, operators can significantly extend the lifespan of submersible water and slurry pumps, ensuring they operate efficiently and reliably. Regular and thorough maintenance prevents unexpected downtime and reduces the overall cost of ownership by minimizing the need for costly repairs or replacements.
Common Mistakes While Buying a Submersible Pump and Tips to Avoid Them:
Purchasing submersible pumps involves careful consideration to avoid common mistakes that can lead to inefficiencies and increased costs. Here are some common mistakes while buying a submersible pump and tips on how to avoid them:
-
Incorrect Sizing and Capacity:
Choosing a submersible pump with inappropriate capacity for the application can lead to inefficiencies such as excessive energy consumption or insufficient flow rate.
Solution: Conduct a detailed analysis of your application’s flow rate and head requirements. Consult with engineers or sales representatives who can provide guidance based on performance curves and system requirements.
-
Neglecting the Liquid’s Characteristics:
Failing to consider the liquid’s characteristics, such as temperature, chemical composition, and solid content, can cause premature wear and tear or pump failure.
Solution: Select a pump material and type suitable for the liquid’s properties. For example, use corrosion-resistant materials for acidic conditions and choose an industrial sump pump for liquids with high solid content.
-
Overlooking the Installation Environment:
Installing the pump in an unsuitable environment can affect its performance and longevity.
Solution: Evaluate the installation site for depth, space, and accessibility. Ensure that the submersible pump is compatible with the environmental conditions, such as submersion depth and temperature.
-
Ignoring Pump Efficiency:
Purchasing a pump with consideration of its efficiency can lead to higher operational costs.
Solution: Look for submersible pumps with high-efficiency ratings and low energy consumption. Review efficiency charts and select a pump that operates most efficiently at your required operating point.
-
Skimping on Quality for Cost:
Opting for cheaper, lower-quality pumps can result in frequent breakdowns and higher maintenance costs.
Solution: Invest in high-quality submersible pumps from reputable manufacturers. While the initial cost may be higher, the long-term savings in maintenance and replacement costs justify the investment.
-
Failing to Consider Future Needs:
Purchasing a pump that meets immediate needs without considering future requirements can limit scalability and adaptability.
Solution: Anticipate potential changes in operational conditions and choose a submersible pump with some capacity to handle increased demands or different operating conditions
Why Invest in Submersible Pumps from EDDY Pump?
Investing in submersible pumps from EDDY Pump offers several key advantages that make them a preferred choice for many industries, including mining, dredging, and wastewater treatment. Here are the most essential points to consider:
-
Patented Technology:
EDDY Pump utilizes a unique, patented EDDY Pump technology that handles more solids and viscous materials than other pumps. This technology ensures minimal clogging and higher production rates, making it ideal for applications dealing with abrasive and challenging materials.
-
Made in the USA:
EDDY Pump proudly manufactures all its submersible pumps in the USA, ensuring high-quality construction and adherence to stringent manufacturing standards. This commitment to American manufacturing also supports the local economy and assures customers of reliable performance and durability.
-
High Efficiency:
The design of EDDY Pumps allows for a higher tolerance of variably sized materials, which contributes to maintaining high operational efficiency. This efficiency results in lower energy consumption and operational costs.
-
Robust and Durable:
EDDY Pumps are built with durability in mind. They can withstand the harsh conditions often found in submersible pumping applications. The robust construction extends the pump’s life and reduces maintenance needs.
-
Versatility:
EDDY Pump’s submersible pumps are suitable for various applications. They are designed to perform efficiently across diverse operational environments, whether handling slurry, sand, or abrasive materials.
-
Reduced Maintenance Costs:
Thanks to their design and materials, EDDY Pumps require less maintenance than conventional pumps. Their ability to handle solids effectively reduces wear and tear, lowering the frequency of repairs or part replacements.
-
Exceptional Customer Support:
EDDY Pump is known for its excellent customer service and support. The company provides detailed guidance on pump selection, installation, and maintenance, ensuring customers achieve optimal performance and longevity from their investments.
Investing in EDDY Pump’s submersible pumps means benefiting from advanced pumping technology that offers high efficiency, durability, and operational cost savings, supported by excellent customer service. These features make EDDY Pump an intelligent choice for those requiring reliable and effective pumping solutions.
Conclusion:
Submersible pumps are the pinnacle of efficiency and reliability in fluid handling. Their versatile applications, durable designs, and minimal maintenance requirements make them indispensable assets across industries worldwide. Submersible pumps offer unparalleled performance, whether draining flooded areas, managing sewage, or handling abrasive slurries. Embrace the power of innovation and invest in submersible pumps for your pumping needs today!