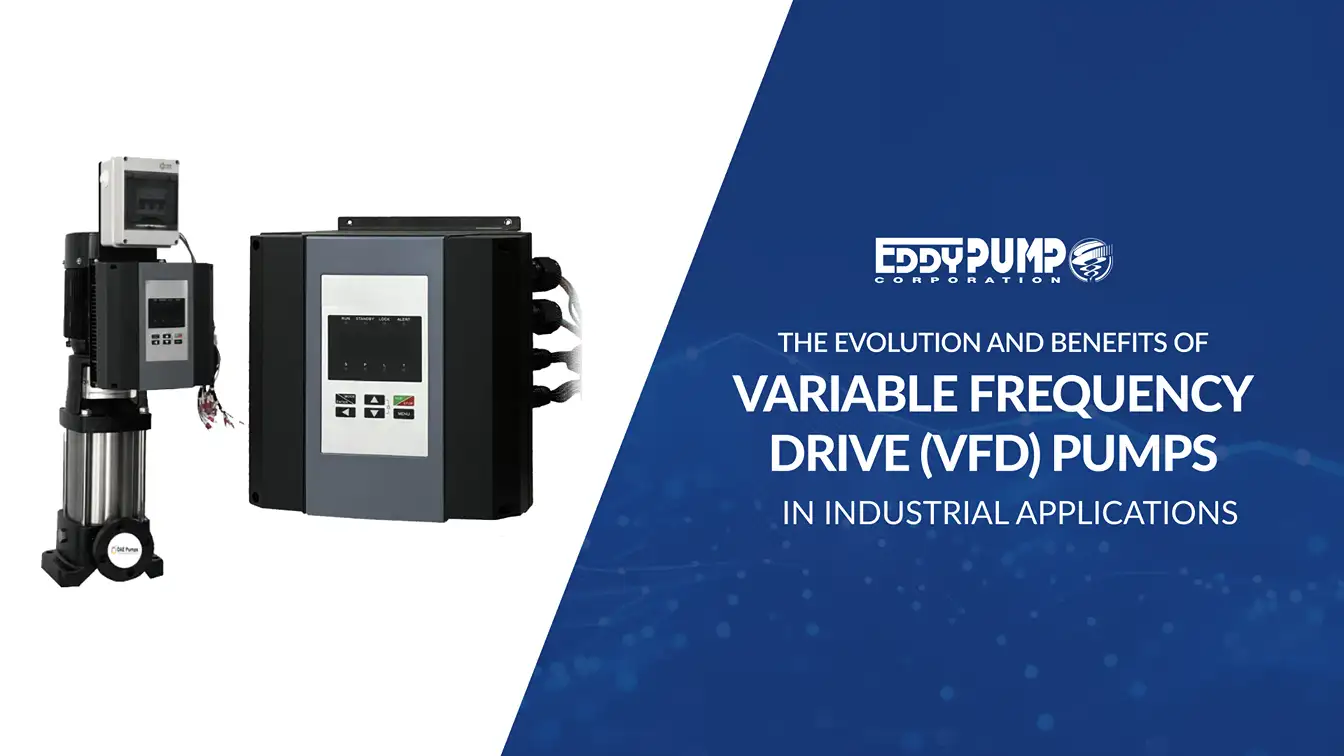
At the core of many industrial processes lies pump technology, which has evolved from simple water-lifting devices in ancient civilizations to the sophisticated machinery we see today. This evolution has been marked by several key milestones, from the Archimedean screw to the centrifugal and positive displacement pumps that powered the Industrial Revolution. One of the most groundbreaking advancements in recent decades has been the development of Variable Frequency Drive, or VFD pumps. These innovative pumps, also known as variable frequency drive pumps, have changed how industries manage fluid handling, offering unparalleled control, efficiency, and adaptability.
The advent of VFD pumps represents a significant leap forward in pump technology. Unlike traditional fixed-speed pumps, VFD pumps are designed to adjust their motor speed in response to varying demands, resulting in substantial energy savings and enhanced operational efficiency. This capability is particularly crucial in today’s industrial environment, where sustainability and cost-effectiveness are paramount. By optimizing the speed of the pump motor, VFD pumps minimize energy consumption, reduce wear and tear on components, and improve process control, making them an indispensable tool across a wide range of industries.
In this blog, we will delve into the history and evolution of pump technology, highlighting the significant milestones that have led to the development of VFD pumps. We will explore the mechanics of these advanced pumps, their industrial applications, and the myriad benefits they offer. By the end of this comprehensive overview, it will be clear why VFD pumps are at the forefront of modern industrial innovation, driving efficiency and sustainability in numerous applications.
What is a VFD Pump?
A Variable Frequency Drive (VFD) pump, also known as a variable frequency drive pump, is an advanced type of pump that utilizes a VFD to control the speed of its motor. This technology enables the pump to adjust its speed in real time based on the specific demands of the system it serves. A VFD pump can optimize its performance by varying the frequency and voltage supplied to the motor, offering superior energy efficiency and operational flexibility compared to traditional pumps.
Definition and Components of a Variable Frequency Drive Pump
A VFD pump consists of several vital components that work together to deliver precise control over the pump’s operation:
- Pump Motor: The electric motor that drives the pump. A VFD pump motor is specifically designed to handle variable speeds.
- Variable Frequency Drive (VFD): The core component that regulates the speed of the pump motor. It converts the fixed-frequency electrical supply into a variable-frequency output, allowing the engine to operate at different speeds.
- Pump Assembly: The mechanical part of the pump, which includes the impeller, casing, and other hydraulic components. This part of the pump remains essentially the same as in traditional pumps.
- Control System: The interface allows operators to set and adjust pump operation parameters. This can include manual controls, programmable settings, and integration with automated systems.
How VFD Pumps Differ from Traditional Pumps
VFD pumps differ from traditional fixed-speed pumps in several significant ways:
- Speed Control: Traditional pumps operate at a constant speed, regardless of the demand. This often leads to inefficiencies, as the pump may run faster than necessary. In contrast, a VFD pump adjusts its speed to match the required flow and pressure, significantly reducing energy consumption.
- Energy Efficiency: VFD pumps consume less energy by varying the motor speed to meet the system’s demands. This results in lower operational costs and a reduced environmental footprint.
- Operational Flexibility: VFD pumps offer greater control over the pumping process. Operators can fine-tune the pump’s performance to meet specific requirements, enhancing the system’s overall efficiency and reliability.
- Reduced Wear and Tear: The ability to adjust speed reduces the mechanical stress on pump components, leading to longer service life and lower maintenance costs.
- Integration with Smart Systems: VFD pumps can be integrated with IoT and other intelligent technologies, allowing for remote monitoring and control, predictive maintenance, and enhanced data analytics.
Additionally, VFD pumps can be optimized for specific applications, such as the vortex pump for handling fluids with solids or the variable speed water pump for applications requiring precise flow control. These specialized pumps further extend the advantages of VFD technology, making them suitable for a wide range of industrial and commercial uses.
Mechanics of Variable Frequency Drive
Understanding the mechanics of a Variable Frequency Drive (VFD) is essential to appreciating its efficiency and flexibility in pump operations. This section delves into how a VFD controls a pump’s motor speed and the relationship between VFD technology, energy consumption, and efficiency.
How VFD Controls the Pump’s Motor Speed
A Variable Frequency Drive pump, commonly called a variable speed water pump, uses a VFD to control the pump motor’s speed precisely. Here’s how it works:
- Input Conversion: The VFD receives a fixed-frequency AC power supply, typically 50 or 60 Hz. This input is first converted into DC (Direct Current) through a process known as rectification. The rectifier component of the VFD performs this conversion.
- DC Bus: The converted DC power is stored in the DC bus, a critical part of the VFD. The DC bus acts as a reservoir, holding the DC voltage steady and supplying it to the inverter.
- Inverter: The inverter then converts the DC power back into AC at a variable frequency and voltage. This process, known as inversion, is managed by switching transistors that adjust the output based on the desired speed and torque requirements.
- Output Control: The VFD’s control system determines the frequency and voltage of the AC output. By adjusting these parameters, the VFD can precisely control the motor’s speed and torque. This is achieved through Pulse Width Modulation (PWM), a technique that modulates the width of the power pulses to control motor speed and performance.
- Feedback Loop: Modern VFD systems often include feedback mechanisms. Sensors monitor the pump’s performance and environmental conditions, providing real-time data to the VFD. This feedback loop allows for continuous adjustments, ensuring optimal performance and efficiency.
Relationship Between VFD, Energy Consumption, and Efficiency
Integrating a VFD into a pump system, such as a vortex or variable speed water pump, significantly improves energy consumption and efficiency. Here’s how:
- Energy Savings: Traditional pumps operate at a fixed speed, which can result in excessive energy use when total capacity is not required. A VFD pump adjusts its motor speed to match the actual demand. The VFD pump minimizes energy consumption by reducing speed during low-demand periods. This dynamic adjustment leads to substantial energy savings, often between 20% to 50% compared to fixed-speed pumps.
- Efficiency Optimization: VFDs enhance overall system efficiency. By controlling the motor speed, the VFD ensures that the pump operates within its optimal performance range. This reduces hydraulic losses and improves the efficiency of the entire pumping process. For instance, VFD pumps maintain efficiency across different operating conditions in applications requiring variable flow rates, such as HVAC systems or irrigation.
- Reduced Mechanical Stress: Operating a pump at variable speeds reduces mechanical stress on the pump components. Fixed-speed pumps often experience high wear and tear due to constant high-speed operation. VFD pumps, by contrast, can operate at lower speeds when total capacity is not needed, extending the pump’s lifespan and reducing maintenance costs.
- Precise Process Control: The ability to adjust motor speed in real time allows for precise control of the pumping process. This is particularly important in applications requiring specific flow and pressure settings. For example, in a water treatment plant, a variable-frequency drive pump can adjust its speed to maintain consistent water pressure, enhancing the reliability and quality of the treatment process.
- Environmental Impact: By reducing energy consumption, VFD pumps contribute to lower greenhouse gas emissions. This aligns with sustainability goals and regulatory requirements, making VFD pumps an environmentally friendly choice for industrial applications.
Industrial Applications of VFD Pumps
Variable Frequency Drive (VFD) pumps, including vortex and variable speed water pumps, have become integral components in various industrial sectors. Their ability to provide precise control, improve energy efficiency, and reduce operational costs makes them highly valuable across different applications. Here, we focus on three key industries that extensively use VFD pumps: water treatment, oil and gas, and mining.
Water Treatment
In the water treatment industry, maintaining optimal flow and pressure is crucial for the efficiency and effectiveness of the treatment process. VFD pumps offer several advantages in this context:
Flow Regulation: Water treatment plants require variable flow rates depending on the time of day and demand. A variable frequency drive pump adjusts its speed to meet these changing demands, ensuring consistent water pressure and flow.
Energy Efficiency: Energy consumption is a significant concern in water treatment facilities. VFD pumps reduce energy use by operating at lower speeds during periods of reduced demand. This lowers energy costs and decreases the plant’s carbon footprint.
Enhanced Control: VFD pumps provide precise control over water treatment processes, such as filtration and chemical dosing. This precision improves treated water quality and ensures compliance with regulatory standards.
Reduced Mechanical Stress: VFD pumps minimize wear and tear on pump components by operating at variable speeds, extending their lifespan, and reducing maintenance costs.
Oil and Gas
The oil and gas industry relies on robust and efficient pumping systems to manage hydrocarbon extraction, transportation, and processing. VFD pumps play a critical role in these operations:
Variable Flow Requirements: In oil and gas extraction, fluid flow rates can vary significantly. A variable-speed water pump can adjust its operation to accommodate these changes, maintaining optimal performance and reducing energy consumption.
Pressure Control: Maintaining precise pressure levels is essential for the safety and efficiency of oil and gas operations. VFD pumps allow for accurate pressure control, reducing the risk of equipment failure and improving overall system reliability.
Energy Savings: The energy-intensive nature of oil and gas operations makes energy efficiency a top priority. VFD pumps help reduce energy consumption by adjusting their speed to match the exact requirements of the process, leading to significant cost savings.
Durability: Oil and gas environments are harsh, requiring high equipment durability. VFD pumps, especially vortex pumps, are designed to handle challenging fluids with solid content, ensuring reliable operation even under demanding conditions.
Mining
Mining operations involve extracting and processing minerals, requiring efficient and reliable pumping solutions. VFD pumps offer numerous benefits in this industry:
Efficient Slurry Handling: Mining processes often involve transporting slurry, a mixture of water and solid particles. VFD pumps, particularly vortex pumps, are well-suited for handling abrasive slurries and ensure smooth and efficient operation.
Optimized Energy Use: Mining sites can experience fluctuating water levels and flow rates. A variable frequency drive pump can adjust its speed to match these variations, optimizing energy use and reducing operational costs.
Improved Process Control: Precise control over pumping operations is crucial in mining. VFD pumps allow for fine-tuning of flow rates and pressures, enhancing the efficiency of mineral extraction and processing.
Enhanced Equipment Lifespan: Mining equipment is subjected to heavy wear and tear. VFD pumps extend the lifespan of pumps and related equipment by reducing mechanical stress through variable-speed operation, lowering maintenance expenses.
Advantages of VFD Pumps
Variable Frequency Drive (VFD) pumps, including vortex pumps and variable speed water pumps, offer several significant advantages that make them essential for modern industrial applications. These benefits include energy savings and operational efficiency, reduced wear and tear on pump components, and improved process control and system performance. Let’s explore each of these advantages in detail.
Energy Savings and Operational Efficiency
One of the primary benefits of a variable frequency drive pump is its ability to provide substantial energy savings and enhance operational efficiency.
- Optimized Energy Consumption: Traditional pumps often operate constantly, leading to unnecessary energy use when total capacity is not required. A variable frequency drive pump adjusts its speed based on real-time demand, ensuring that it uses only the necessary energy. This adjustment can result in up to 50% of energy savings, making VFD pumps an economically and environmentally beneficial choice.
- Reduced Operating Costs: Lower energy consumption directly translates to reduced operating costs. By integrating VFD pumps into their systems, industrial facilities can significantly decrease energy bills. This is particularly beneficial in energy-intensive industries such as water treatment, oil and gas, and mining, where energy costs represent a substantial portion of operational expenses.
- Enhanced Efficiency: VFD pumps are designed to operate efficiently across various conditions. By maintaining optimal speed and performance, these pumps ensure that energy is not wasted through over-pumping or under-pumping, further enhancing overall system efficiency.
Reduced Wear and Tear on Pump Components
The ability of a variable frequency drive pump to adjust its speed also contributes to the longevity and reliability of the pump components.
- Minimized Mechanical Stress: Traditional pumps operating at constant high speeds experience significant mechanical stress, leading to accelerated wear and tear on components. VFD pumps, by contrast, can operate at lower speeds when total capacity is not required, reducing mechanical stress and extending the pump’s and its components’ life.
- Lower Maintenance Costs: With reduced wear and tear, VFD pumps require less frequent maintenance and fewer repairs. This lowers maintenance costs and minimizes downtime, ensuring that industrial processes remain uninterrupted and efficient.
- Smooth Start and Stop Cycles: VFD pumps offer the advantage of smooth start and stop cycles. Traditional pumps can cause water hammer and pressure surges during start-up and shut-down, damaging pipes and other system components. VFD pumps gradually increase and decrease speed, preventing these issues and reducing wear and tear on the system.
Improved Process Control and System Performance
The precision and flexibility of a variable frequency drive pump significantly enhance process control and overall system performance.
- Precise Flow and Pressure Control: VFD pumps allow for precise control over flow rates and pressure levels, making them ideal for applications that require exact specifications. For example, maintaining consistent pressure and flow is crucial for optimal filtration and chemical dosing in water treatment processes. VFD pumps ensure that these parameters are accurately controlled, improving process outcomes.
- Adaptability to Variable Conditions: Industrial processes often involve variable conditions that require pumps to adapt quickly. A variable-speed water pump can respond to changes in demand, environmental conditions, and system requirements in real-time. This adaptability ensures that the pump operates efficiently and effectively under all conditions.
- Enhanced System Integration: VFD pumps can be easily integrated into existing control systems, including IoT and innovative technology. This integration allows for advanced monitoring, diagnostics, and control, enabling operators to optimize pump performance and address issues proactively. Remotely monitoring and adjusting VFD pumps enhances system reliability and performance.
- Improved Reliability: By operating within their optimal performance range and avoiding the extremes of constant high-speed operation, VFD pumps experience fewer failures and disruptions. This reliability is crucial in critical applications such as oil and gas extraction, where pump failure can lead to significant operational and financial losses.
Case Studies Demonstrating Advantages
- Water Treatment Facility: A municipal water treatment facility replaced its fixed-speed pumps with VFD pumps. The upgrade resulted in a 40% reduction in energy consumption, lower maintenance costs due to reduced wear and tear, and improved control over water pressure and flow, enhancing the overall treatment process.
- Oil Refinery: An oil refinery integrated variable frequency drive pumps into its system to manage variable flow rates and pressures. The VFD pumps provided precise control, reducing energy consumption by 30%, minimizing equipment wear, and improving the reliability and efficiency of the refinery’s operations.
- Mining Operation: A mining company dealing with abrasive slurry utilized vortex pumps with VFD technology. The VFD pumps handled the challenging slurry efficiently, reducing downtime and maintenance costs by 50%, optimizing energy use, and enhancing overall productivity.
Integrating VFD Pumps into Existing Systems
Integrating Variable Frequency Drive (VFD) pumps into existing systems can significantly enhance performance, efficiency, and longevity. This section will cover the steps for retrofitting traditional pumps with VFD technology and considerations for seamless integration, ensuring the optimal use of VFD pumps, variable frequency drive pumps, vortex pumps, and variable speed water pumps.
Steps for Retrofitting Traditional Pumps with VFD Technology
Assessment of Current System:
- Evaluate Pump Performance: Assess the performance of the existing traditional pumps. Identify inefficiencies, such as energy wastage, inconsistent flow rates, and maintenance issues.
- Determine Compatibility: Ensure the current pump and motor are compatible with VFD technology. Most standard AC motors can be retrofitted with a VFD, but it’s essential to verify compatibility to avoid technical issues.
Selection of Appropriate VFD Pump:
- Choose the Right VFD: Select a VFD pump that matches the specifications of your current system. Consider factors such as the required flow rate, pressure, and specific application needs. Vortex pumps are ideal for handling abrasive or slurry materials, while variable-speed water pumps are suited for applications requiring precise flow control.
- Consider VFD Features: Look for features that enhance performance, such as programmable controls, real-time monitoring, and integration capabilities with existing control systems.
Installation of VFD Pump:
- Electrical Installation: Connect the VFD to the existing motor and electrical system. Ensure that the installation complies with local electrical codes and standards.
- Programming and Configuration: Program the VFD according to the system requirements. This includes setting parameters such as speed, acceleration, deceleration, and safety limits.
- Integration with Control Systems: Integrate the VFD with existing control systems. This may involve connecting the VFD to a central control unit, SCADA system, or other monitoring tools to enable seamless operation and real-time data collection.
Testing and Calibration:
- Initial Testing: Conduct initial tests to ensure the VFD pump operates correctly within the system. Check for incorrect speed settings, electrical faults, or mechanical problems.
- Calibration: Fine-tune the VFD settings to match the application’s exact requirements. This may involve adjusting speed ranges, pressure limits, and response times to optimize performance.
Training and Documentation:
- Operator Training: Train operators and maintenance personnel on the new VFD system. Ensure they understand operating, monitoring, and maintaining the VFD pump effectively.
- Documentation: Maintain comprehensive documentation, including installation procedures, programming settings, maintenance schedules, and troubleshooting guides.
Considerations for Seamless Integration
Compatibility and System Requirements:
- Motor Compatibility: Ensure the existing motor is compatible with VFD technology. If the motor is unsuitable, consider replacing it with one designed for VFD use.
- System Capacity: Evaluate the system’s electrical capacity to handle the additional load from the VFD. Ensure the power supply, wiring, and circuit breakers can support the VFD without overloading.
Environmental Factors:
- Temperature and Ventilation: VFDs generate heat during operation. Ensure adequate ventilation and cooling to prevent overheating. Install VFDs in environments with controlled temperatures to maintain optimal performance.
- Dust and Moisture Protection: Protect the VFD from dust, moisture, and other environmental factors affecting its performance. Use enclosures or protective covers if necessary.
Control and Monitoring Integration:
- Communication Protocols: Ensure the VFD supports the communication protocols used by the existing control system. Standard protocols include Modbus, Profibus, and Ethernet/IP.
- Real-Time Monitoring: Integrate the VFD with monitoring systems to provide real-time data on performance, energy consumption, and potential issues. This allows for proactive maintenance and quick response to any anomalies.
Safety and Compliance:
- Safety Features: Ensure the VFD has overcurrent protection, fault detection, and emergency stop functions.
- Regulatory Compliance: Verify that the VFD installation complies with relevant industry standards and regulations, including electrical codes, safety standards, and environmental guidelines.
Maintenance and Support:
- Regular Maintenance: Implement a regular maintenance schedule to keep the VFD pump in optimal condition. This includes inspecting electrical connections, cleaning filters, and updating software.
- Technical Support: Establish a VFD manufacturer or supplier support plan. This ensures access to technical assistance, spare parts, and updates when needed.
Optimizing Performance with VFD Technology
Optimizing the performance of Variable Frequency Drive (VFD) technology involves implementing best practices for efficiency and longevity alongside regular maintenance and monitoring. This ensures that VFD, variable frequency drive, vortex, and variable speed water pumps operate at peak performance, providing maximum benefits.
Best Practices for Maximizing Efficiency and Longevity
Proper Sizing and Selection:
- Accurate Sizing: Ensure the VFD pump is appropriately sized for the application. Oversized or undersized pumps can lead to inefficiencies, increased wear, and higher energy costs. Use precise calculations based on flow rates, pressure requirements, and system dynamics.
- Application-Specific Selection: Choose the correct type of VFD pump for the specific application. Vortex pumps are ideal for handling slurry and abrasive materials, while variable-speed water pumps are better suited for applications requiring precise flow control.
Optimized Settings and Programming:
- Custom Programming: Program the VFD with settings that match the operational requirements. This includes adjusting speed ranges, acceleration and deceleration times, and safety limits. Tailoring the settings to the specific application can significantly enhance efficiency and performance.
- Energy-Saving Modes: Utilize energy-saving modes and features available in modern VFDs. These modes can automatically adjust the pump speed based on demand, reducing energy consumption during low-load periods.
Effective Load Management:
- Load Matching: Match the VFD pump’s output to the system’s load requirements. Avoid running the pump at full speed when the demand is low. Implementing variable speed control helps in maintaining optimal performance while reducing energy use.
- Avoiding Overloads: Prevent overloading the pump by monitoring operational parameters and ensuring the system does not exceed the pump’s designed capacity. Overloads can cause excessive wear and potential damage to both the pump and the VFD.
Quality Installation:
- Professional Installation: Ensure the VFD pump is installed by qualified professionals. Proper installation includes correct electrical connections, appropriate placement, and compliance with safety standards. Poor installation can lead to operational issues and reduced lifespan.
- Environmental Considerations: Install the VFD in an environment that protects it from extreme temperatures, dust, and moisture. Proper ventilation and cooling systems should be in place to prevent overheating.
System Integration:
- Seamless Integration: Integrate the VFD pump with existing control systems for coordinated operation. This includes connecting to SCADA systems, programmable logic controllers (PLCs), and other real-time data acquisition and control monitoring tools.
- Communication Protocols: Ensure compatibility with Modbus, Profibus, or Ethernet/IP, facilitating smooth interaction with other system components.
Regular Maintenance and Monitoring Tips
- Visual Checks: Perform regular visual inspections to identify signs of wear, damage, or leaks in the VFD pump and associated components. Early detection of issues can prevent major failures and costly repairs.
- Electrical Connections: Inspect electrical connections for signs of corrosion, loose fittings, or overheating. Ensuring secure and clean connections is vital for reliable operation.
- Performance Monitoring: Continuously monitor key performance parameters such as flow rate, pressure, and energy consumption. This data helps identify trends, diagnose issues, and make informed decisions about adjustments.
- Vibration Analysis: Conduct regular vibration analysis to detect imbalances, misalignments, or bearing wear. Vibration monitoring is crucial for detecting mechanical issues that could lead to pump failure early.
- Scheduled Maintenance: Follow a preventive maintenance schedule that includes cleaning filters, checking lubrication, and replacing worn parts. Regular maintenance ensures that the VFD pump operates efficiently and extends its lifespan.
- Software Updates: Keep the VFD’s software and firmware updated to take advantage of the latest features, improvements, and bug fixes provided by the manufacturer.
- Real-Time Monitoring: Implement condition-based maintenance by utilizing real-time monitoring tools and sensors. This approach allows maintenance based on the actual condition of the VFD pump rather than on a fixed schedule.
- Predictive Analytics: Employ predictive analytics to forecast potential issues based on historical data and operating conditions. Predictive maintenance can prevent unexpected failures and optimize maintenance intervals.
- Operator Training: Ensure operators and maintenance personnel are trained on the VFD pump’s operation, settings, and maintenance procedures. Knowledgeable staff can effectively manage the system and respond to issues promptly.
- Comprehensive Documentation: Maintain detailed documentation of the VFD pump’s installation, settings, maintenance records, and any modifications. This information is valuable for troubleshooting and future upgrades.
- Protective Measures: Implement protective measures to shield the VFD pump from adverse environmental conditions. This includes using enclosures, ensuring proper ventilation, and controlling humidity and temperature levels.
- Regular Cleaning: Keep the VFD and its surroundings clean to prevent dust accumulation and contamination. Dust can interfere with cooling systems and electrical connections, affecting performance.
Conclusion:
Variable Frequency Drive (VFD) pumps have revolutionized how industries manage their pumping systems, providing substantial benefits and underscoring their importance. VFD pumps offer unparalleled energy savings, enhanced operational efficiency, and reduced wear and tear on pump components by controlling the motor speed and adjusting to the precise demands of various applications. These advantages translate into significant cost savings and improved system performance, making VFD pumps an indispensable asset in the water treatment, oil and gas, and mining sectors.
Looking ahead, the future potential of VFD pump technology is immense. Advancements in VFD technology are poised further to enhance the efficiency and functionality of pumping systems. Innovations like integrating the Internet of Things (IoT) and intelligent systems will enable real-time monitoring and predictive maintenance, ensuring greater reliability and reduced downtime. The continuous development of more sophisticated control algorithms and energy-saving features will further cement the role of VFD pumps in promoting sustainability and environmental responsibility.